The First Aluminum Automobiles
Used as part of automotive and light weight truck framework
The first sports car featuring an aluminum body was presented at the Berlin International Motor Show in 1899; the first engine with aluminum parts was made 2 years later when in 1901 Karl Benz, of Benz and Company, which would become Mercedes Benz, presented a new car for the prestigious race in Nice (France). As with the yacht Defender, the lightweighting provided by aluminum added to the successful performance of the car, but difficulties in metal working, lack of knowledge and the high price of aluminum prohibited its use in early mass production.
Cast aluminum transmission housings and pistons have been commonly used in cars and trucks since the early 1900’s. Aluminum and aluminum alloys appeared on the 1908 Bugatti, whose construction included extensive aluminum sand castings and formed aluminum body panels that were butt-welded with the use of the oxy-fuel torch and hand-worked to a polished condition.
Pierce Arrow bodies were cast for several years – from 1912 until 1917 or 1918. The cast bodies were enormous sand castings and were often welded as part of the assembly process. The casting thickness was between 1/4 and 1/8 in. thick, and the bodies were of good appearance, durable and structurally sound.
The six-cylinder engines produced by Pierce-Arrow were cast in pairs and secured to aluminum crankcases. Europeans in particular were very fond of aluminum and, during the 1920’s and 1930’s, made quite artistic automotive bodies using the material.
Beautiful limited production custom and racing coachwork for automobiles of the 1930’s exhibited extremely fine aluminum metal art work that reached its pinnacle during this period.
Today, cast products, primarily engine and other under-the-hood components make up more than half of the aluminum used in cars.
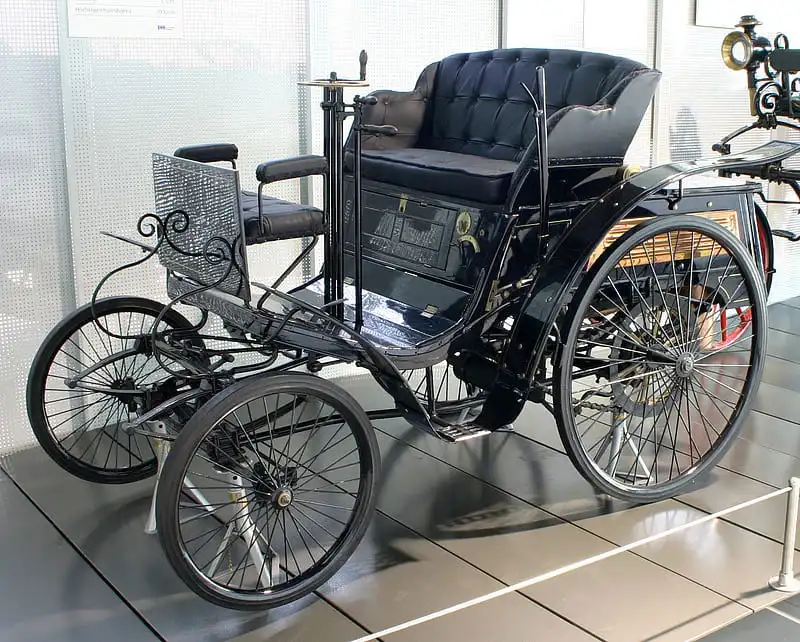


Photos of various aluminum automobiles including the 1901 Benz, the 1908 Bugatti, and the 1917 Pierce Arrow.
Lightweighting, driven by aluminum’s extraordinary high strength-to-weight ratio, continues to be an important requirement in the automotive industry today. The 5000 series alloys are popular candidates to fill the rapidly growing need for automotive structural sheet. In these applications, strength and corrosion resistance are needed but formability is also an important requirement. Today, 6000 series extrusions are in use as part of automotive and light weight truck framework. Anodizing is becoming the finish of choice for bonding applications where tolerances are tight and standard fasteners cannot be used.